Nano-coatings are being used all the time to protect electronic circuit board assemblies.
This is because the base materials they are formulated from are fluorinated polymers that have very different properties to traditional conformal coatings.
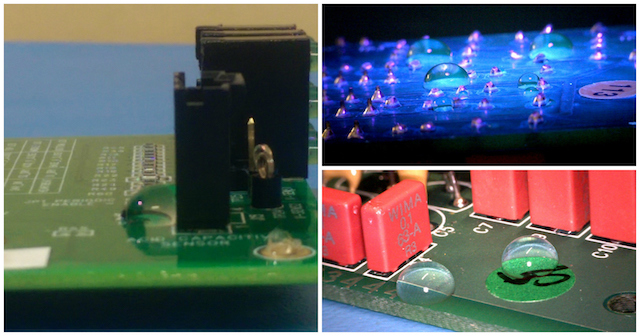
So, how are the Nano-coatings different to conformal coatings?
To understand the properties of a Nano-coating you have to understand what a fluoropolymer coating is made of.
Typically, the material is comprised of fluorocarbons and characterized by carbon-fluorine bonds. Therefore, the film surface
is not susceptible to Van der Waals forces (interfacial electrostatic bonds).
This means the surface energy of the fluoropolymer coating is extremely low and the surface of the circuit becomes
hydrophobic. That is the Nano-coating is highly water repellent and acts like Teflon on a frying pan.
This water repellency (non-wetting of water) on the circuit board is one of the most important properties making the
Nanocoatings so popular.
What other key properties do Nano-coatings have that may help protect circuit boards?
For electronic circuits, there are several key properties that can be extremely useful.
These include being:
• Hydrophobic: The coating is highly water repellent.
• No masking required: Protection whilst being extremely thin meaning no masking is required on nearly all component parts (see below).
• High moisture barrier: The Nano-coatings generally have a low water vapor transmission rate that provides excellent corrosion resistance.
• Chemically resistant: Fluorinated coatings have a high chemical resistance that helps protect the circuits.
• Good dielectrics: fluoropolymer coatings have high dielectric properties
However, to really understand another key benefit of using a Nano-coating you have to look at the main difference of the thin film compared to a conventional conformal coating.
That is that no masking is normally required when applying the Nano-coating.
Why do you not need to mask components on a circuit board when using a Nano-coating?
A normal conformal coating is applied at typical thicknesses of 25um or more.
This thickness makes it quite a hard coating with considerable mar resistance (resistance to abrasion).
Significant force is required to remove the coating. Pushing male and female connector parts together would not remove the coating from the mating pins.
However, this is not a problem for a Nano-coating.
Since the Nano-coating can be applied at ultra-thin thicknesses (typically 1-2um in thickness) without any protection performance reduction, then the thin coating is easily removed or scratched away when the connectors are joined and the electrical circuit is easily made.
This key parameter of not requiring masking during Nano-coating application combined with the hydrophobic nature of the coating material makes the Nano-coatings highly effective in protecting electronic circuit boards at a very low cost per unit.
Ask us how we can help you with your Nano-coating requirements?
Talk to us about your project. See how we can save you money now.
We have the knowledge, tools, experience and the complete solutions whatever you need. We are here to help.
Contact us now.