Why protecting LEDs with a coating is a challenge
Protecting LEDs with a protective coating is big business. The volume of manufactured LEDs globally is growing at an exponential rate and there is no end in sight.
However, the challenges to protect the LEDs themselves with the right coating are not insignificant especially in an outdoor environment.
Although there are many issues in protecting LEDS there are two key problems that really must be considered when selecting a coating.
First, when applying a coating to a LED you must not fundamentally affect the performance of the device.
It’s great that once you apply the film you can protect it from the elements. But, if for example the film interferes with the light transference (less light passes through the film) or is unstable in UV so changes color or degrades then the film is unsuitable.
So, selecting a coating that does not degrade or interferes with the LED is the first challenge.
The second problem is cost.
LED manufacture cost is tumbling all the time. Yet, the cost of coating can be high.
So, the second challenge is to select a coating process that is cost effective.
This leaves the ultimate conundrum. How to balance the cost of materials and process versus the protective properties and this is the key challenge.
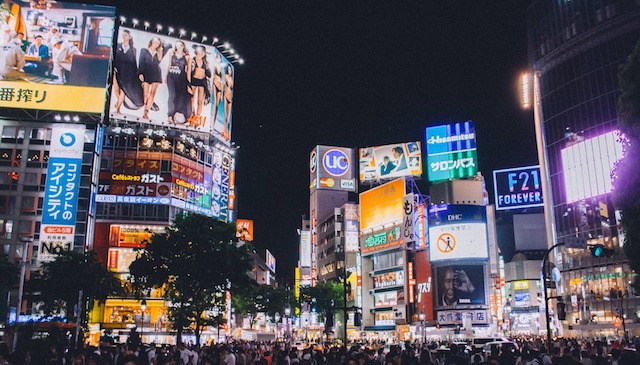
So, lets consider the current coating materials available for protecting LEDs
At this time there are a range of coating options available to protect LEDs.
They include conformal coatings, ultra thin Nano-coatings and fluoropolymer, vapor deposited materials like Parylene and thick film materials like potting compounds and encapsulates.
They vary from less than 1um in film thickness right up to very thick film deposits that completely encapsulate the LEDs.
However, they all have some compromise as part of the selection procedure.
For example, the thick films like encapsulates offer great barrier protection. But, they can affect light transmission, be expensive to buy and also expensive to apply if masking is required.
At the other end of the spectrum are the thin films.
The ultra thin coatings are low cost. But, their protective performance is much less effective compared to the other thicker films.
Increasing the thickness of the thin films (conformal coatings and Parylene) tends to improve the performance. But, now you have to consider the influence on the LED for film transparency and the cost of process if masking is requires.
This makes the selection of materials challenging.
So, is there an alternative protective coating for LEDs besides the current materials?
We at Thin Film Partners have been examining a new novel technique taken from another industry that may be able to meet all of the environmental demands for LEDs and actually be cost-effective.
The process we have been investigating is a hybrid technique of using alternating layers of Atomic Layer Deposition (ALD) and Chemical Vapor Deposition (CVD) films to build an ultra-thin, multi-layer, hybrid coating with a final hydrophobic coating to finish.
This method of using multiple layers of ultra-thin coatings with differing properties, allows us to build a completely different hybrid protective film.
So how does the hybrid film differ to traditional materials for protecting LEDs?
First, the hybrid coating protective performance has been found to be superior to all of the thin films in most categories of testing so far. It provided both improved electrical and physical properties that protect the circuits.
A major issue for LEDs is light loss when the film is applied over the LEDs. For the hybrid coating the coating shows zero loss of light and this is a great advantage.
Also, the material is both temperature and UV stable. The coating will survive up to 350C and does not degrade in UV light. Again, these are great advantages for the performance of the hybrid coating for protecting LEDs.
It is also hydrophobic. This property ensures the LEDs reject water from the surface and improves the film properties enormously.
However, what makes this coating exceptional is its final property.
That is the coating does not require the circuit board to be masked when the coating is being applied!
So, why does the hybrid film not need masking like other traditional conformal coatings and Parylene?
The difference is film thickness.
The hybrid film is much thinner than the other traditional coatings including Parylene. Typical film thicknesses can be as low as 0.1um.
Since the coating is extremely thin it has been found that no masking is required.
This is because when components like connectors are joined together then the ultra-thin coating does not prevent electrical connection. The component mating parts connect together perfectly well and no loss of connection can be measured.
Even better, the physical protection of the film is not compromised. In fact, all of the components including connectors are protected.
This means that the cost of the whole process is purely the cost of materials and the application of the material and nothing else.
Since the process is relatively low cost then this does offer a very interesting alternative to the traditional coating materials in LED processing.
Doesn’t a hybrid ALD / CVD process sound complex to operate?
Actually, although the technology and chemistry can be a little complex the process itself is fairly simple.
Once the process is set up in the machine the operator just loads the LEDs, switches the machine on, waits for the coating to be applied and unloads the LEDs on completion.
This is a far cry from the sophisticated processes of robotic selective coating or the challenges of Parylene.
Further, the application process is actually very stable. In reality this technology is tried and test in other industries for a long period of time and this is just adapted technology.
So what does a hybrid ALD / CVD film look like?
As explained earlier the film is built up of alternating layers of ALD and CVD thin coating layers. The ALD is a ceramic-based material providing the insulating properties and the CVD organic film provides the barrier protection.
Once the required film thickness is achieved then a final hydrophobic layer is applied that combines with the ALD and CVD layers to provide a highly effective barrier.
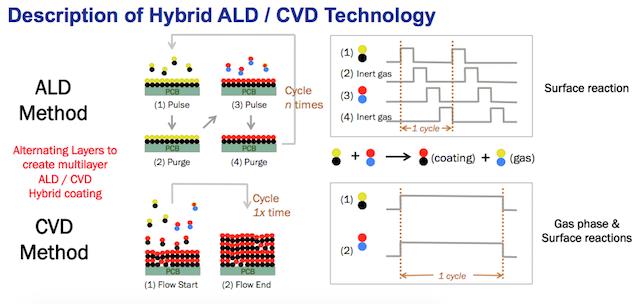
So just how well did the hybrid coating perform in protecting LEDs?
First of all the tests were carried out on live LED circuits from a customer. The customer product was for an outdoor application.
For testing the customer used in-house test methods to prove the technology.
The LED circuit was exposed to environmental tests for resistance against salt, moisture and temperature.
The test methods included:
- Submersion in DI water dip for 12 hours
- Submersion in 25% concentration saltwater dip for 17 hours
- 2 x 6 hour cycles in water ramped from room temperature to 70°C
After each test the boards were tested for failure or problems.
The LED circuit passed on all tests.
Further, all results achieved were completed with no masking of components and zero light loss in LED opacity.
The electrical connections were found to be excellent and the coating did not affect the integrity of the connectors.
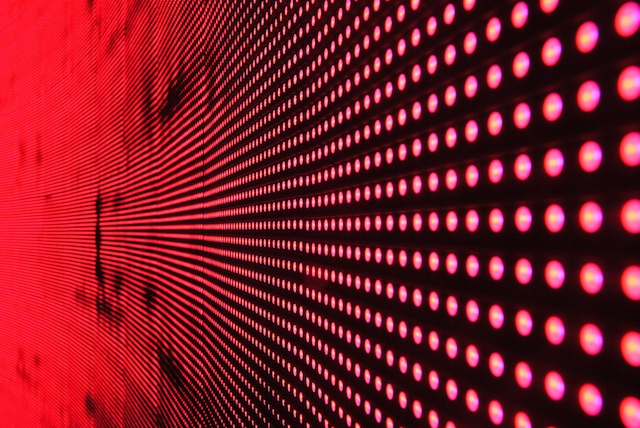
So what about the cost of process?
Since the whole production process is masking and de-masking free then the cost per unit is incredibly low.
Further, the protective properties of the hybrid coating in nearly all cases is superior to the conventional methods.
So, you get a lower cost coating with a higher technical performance.
So, just how good is the hybrid coating as a protective material for LED circuits?
Generally, with protective coatings for electronics then Parylene is considered the gold standard in most cases.
So, we compared Parylene with the hybrid ALD / CVD material.
Property | Parylene | ALD/CVD Coating |
Hardness | Soft | Hard |
Wear resistance/Handling Ease | Poor | Excellent |
Water Vapor Transmission Rate | Good | Excellent |
Temperature Resistance (extended time) | 100°C | 350°C |
Color | Gray/white | Clear |
Adhesion to various materials | Poor | Excellent |
Scalable to large production | Poor | Excellent |
Process Time | 8 – 12 hrs. | 8 – 12 hrs. |
Hydrophobicity | Good | Good – Excellent |
Cost | High | Low – Med |
What we also identified for the material were some key properties for LEDs.
- The Water Vapor Transmission Rate (WVTR) is superior to Parylene so the hybrid coating is far more waterproof for the LEDs.
- Coating adhesion is superior to Parylene and other coatings as the hybrid material covalently bonds to the substrate. So, the lifetime of the material will be better on the circuit.
- The hybrid coating is UV stable whereas Parylene in general is not. This is an important criteria for coatings exposed outside on LEDs
- The hybrid coating stayed 100% transparent during testing (no loss of lux). That again is important for LEDs.
- The coating thickness of the hybrid material is x10 LESS than the Parylene. This aids light transmission and electric connectivity
So, in reality the hybrid ALD / CVD material could just be what the LED industry is looking for in protecting their circuits.
In future articles we will let you know how the material performs on other types of circuits as we have a lot of interest from other areas of the electronics industry.
Need to find out more?
For further information on the hybrid ALD / CVD materials then contact us directly. We can help you trial the coating.
Or, check out the Nexus article, Coating LEDs with a hybrid ALD / CVD Process.